1简介
本文主要介绍了国内某件DCT双离合变速箱在耐久试验过程中发生失效,使用德国红蚂蚁蚂蚁公司(red-ant)的早期故障诊断系统MIG16 SFE实时检测及诊断分析故障零零件的过程。
整个耐久试验过程中MIG16 SFE全程实时监测变速箱内部各零部件振动的异常变化,当试验进行到2015年6月27日06:00:30时发出了中断报警信号;工程师重新启动和运行台架,进行故障复现,于07:04:30将台架停机。
通过对测试数据的分析,诊断和定位故障零部件为输出轴上的三档齿轮。工程师对相应部位进行拆解和检查后,发现的故障零部件与MIG16 SFE诊断分析结果相一致。
2被试件
在MIG16 SFE中通过OrderCalc软件模块对变速箱内部结构及齿轮传动关系进行建模,如图1所示。
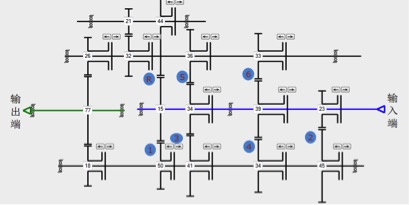
图1 被试件内部结构及档位情况
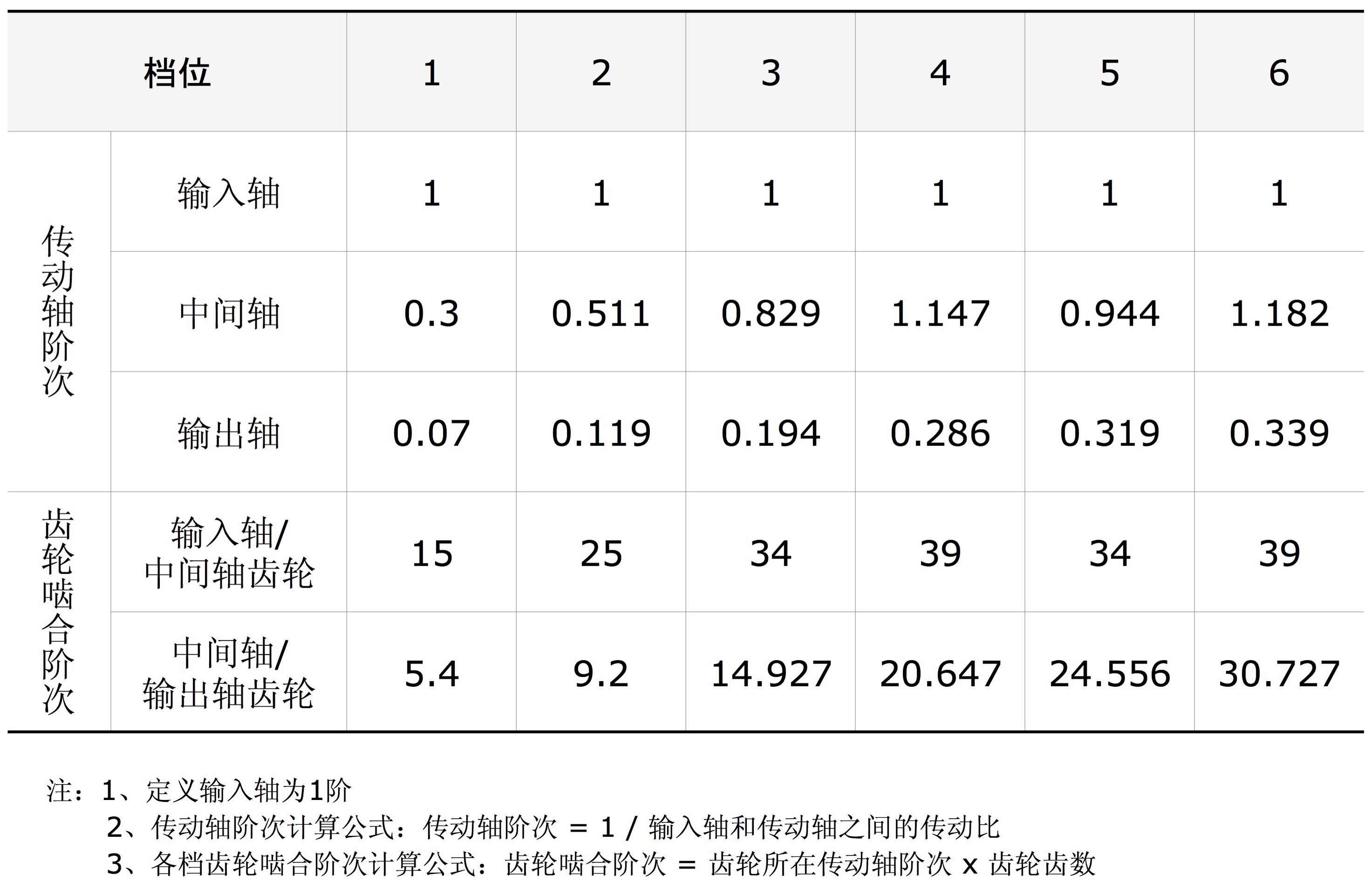
表1 各档位下传动轴及齿轮啮合阶次
3 MIG16 SFE系统设置
3.1硬件设置
根据该变速箱及其试验台架的具体情况,MIG16 SFE的硬件及接口设置如下:
数据采集:24位精度,每通道51.2kHz采样率
振动传感器:数量1个,量程500g,通过胶粘方式固定在变速箱上
输入转速信号:接入驱动电机的转速,TTL频率信号
输出转速信号:接入负载电机的转速,TTL频率信号
变速箱输入扭矩:电压信号
变速箱油温:电压信号
报警输出:继电器开关量
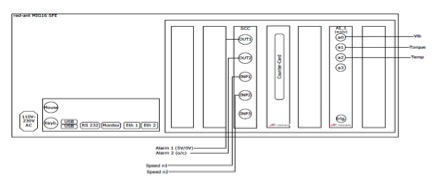
图2 MIG16 SFE与台架接口定义
3.2 软件设置
3.2.1 阶次参数设置
根据表 1 所示的变速箱阶次计算结果,在 MIG16 SFE 软件中对阶次分析的参数进 行设置。
1. 阶次范围
表 1 中出现的最大阶次为 39 阶,阶次分析的范围需包含它的多个谐波(基频的整 数倍),因此设置为 0 ~240 阶。
2. 阶次分辨率
表 1 中出现的最小阶次为 0.07 阶,并且阶次数值精确到小数点后 3 位,为了准确 区分各零部件的阶次,分辨率设置为 0.007 阶。
3.2.2 试验工况设置
针对本次试验的具体情况,在 MIG16 SFE 软件中对转速、扭矩、档位和油温工况 进行设置。
档位:该变速箱为 6 档,将速比划分为 6 个区间。
输入转速:根据试验大纲规定的最高转速和该变速箱的最高转速,设置转速范围为 200 ~ 6000 rpm,划分为 29 个区间。
输入扭矩:根据试验大纲规定的最大扭矩和该变速箱的最大扭矩,设置扭矩范围为 0 ~ 400 rpm,划分为 20 个区间。
油温:划分为 3 个区间,以区分高温、中温、低温等情况。
具体设置如图 3 所示。因此,基于转速、扭矩、档位和油温这四个维度的工况总数为 6 x 29 x 20 x 3 = 10,440,覆盖了整个试验的全部工况。 任何一个工况以一个数组来表示,如(2,10,5,3)表示第 2 个档位区间、第 10 个输入转速区间、第 5 个输入扭矩区间和第 3 个温度区间。
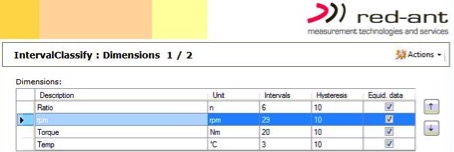
图3 工况区间划分
4 数据分析及故障诊断
4.1 全工况测试数据总览
本次耐久试验自 2015 年 6 月 23 日开始,至 2015 年 6 月 27 日结束。整个试验 的完整情况即全工况测试数据如图 4 所示。其中,n1 为变速箱输入转速,Ratio 为变 速箱输入/输出转速的传动比,Torque 为输入扭矩,OS 为振动阶次检测指标,Vib 为 振动均方根值检测指标。
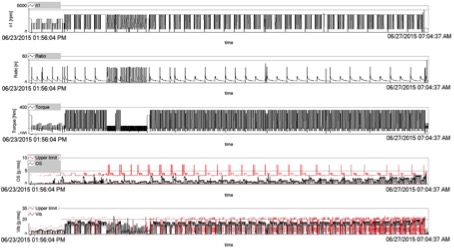
图4 全工况监测数据总览
上图中红色线为检测指标的上下限值,该限值由 MIG16 SFE 系统软件自学习生成。
整体上看, OS 及 Vib 两个检测指标在整个试验过程中均在上下限值之间,直到试验 最后时刻,两个指标都超出了限值,从而触发了停机报警。
4.2 报警工况测试数据分析
对图 4 中检测指标最后超限时刻的数据进行工况滤波,报警时的试验工况为 4.20.15.0(数字所代表的含义参看本文第 3.2.2 节),只提取和显示该工况下的测试 数据总览,如图 5 所示。
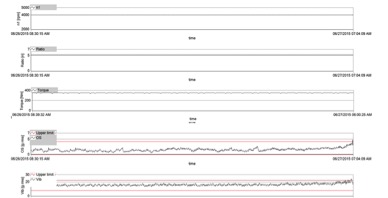
图5 报警工况测试数据总览
该试验工况的转速为 4000rpm,传动比为 5.15(即第三档),扭矩为 380Nm 左右。OS 阶次和 Vib 均方根值检测指标在试验前期整体趋势平稳,但在试验后期呈现明 显增长趋势,最后超出了上限值。
已知输入轴转速 4000rpm 及该 DCT 变速箱的三档齿数,参照表 1 的阶次计算结 果,三档时各传动轴的阶次、转速、频率及每转一圈所需时间如表 2 所示。
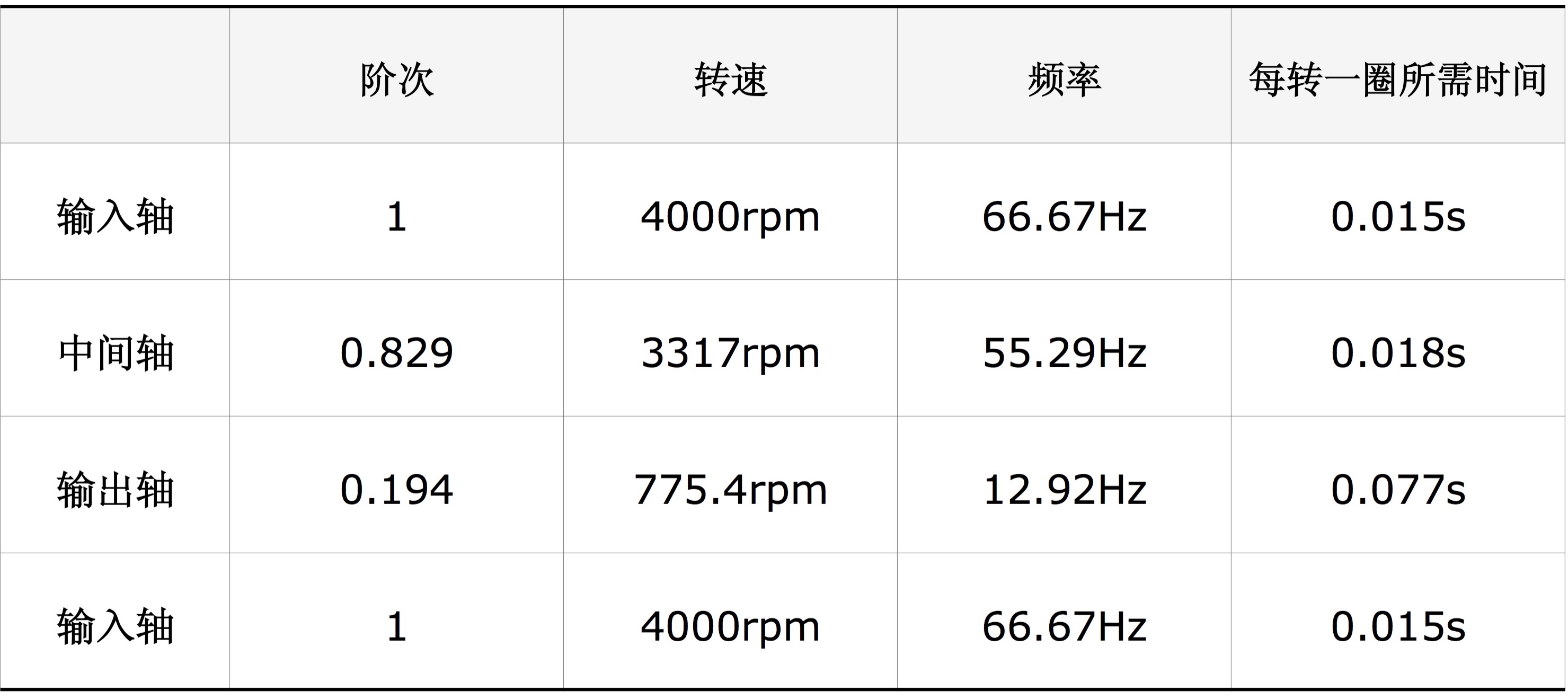
表2 变速箱三档时各传动轴情况
停机报警前四分钟的全部测试数据如图 6 所示。Vib 检测指标自 05:57:52 超上限 报警后,多次频繁超限,最后于 06:00:30 发出停机报警;OS 检测指标也明显增长并 于 06:00:20 超上限报警。
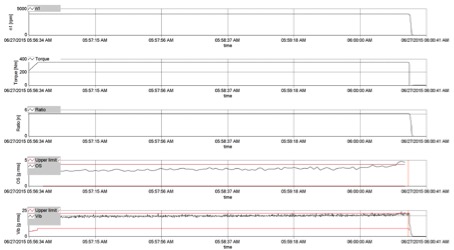
图6 报警前四分钟测试数据
4.3 振动原始信号分析
在 MIG16 SFE 系统软件中对采集和记录的振动原始信号进行分析和回放,停机报警前 2 秒的 Vib 均方根值检测指标和振动原始信号如图 7 所示。
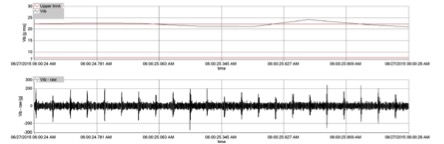
图7 报警时振动原始信号
从振动原始信号中可以明显地看到周期性的振动冲击现象,峰值达到约 200g,峰 值间隔时间为 0.077s。对比表 2 可以发现,该周期时间与输出轴每转一圈的时间 0.077s 相吻合。据此可以判断,故障发生在该输出轴上。
4.4 报警工况三维阶次谱
为进一步诊断和定位故障零部件,对变速箱的振动数据进行阶次分析。提取故障工 况 4.20.15.0 下的 3D 阶次谱,见图 8。图中 x 轴(横向)为阶次,y 轴(纵深方向) 为时间,z 轴(高度方向)为幅值,单位为 g。
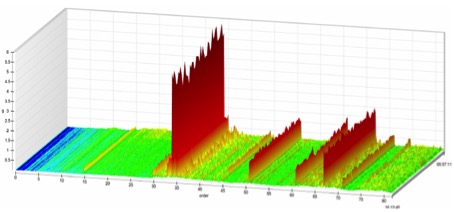
图8 报警工况3D阶次谱
根据图 1 变速箱结构和表 1 阶次计算结果,三档时的啮合齿轮副分别为:
输入轴和中间轴的齿轮副 34/41,齿轮啮合阶次为 34 阶,见图中蓝框;
输入轴和中间轴的齿轮副 18/77,齿轮啮合阶次为 14.927 阶,见图中红框。 分别将 34 阶及 14.927 阶周边的 3D 阶次谱放大,见图 9 及图 10。
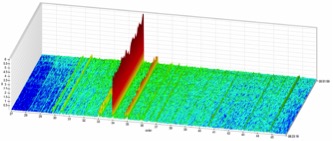
图9 34阶周边的3D阶次谱
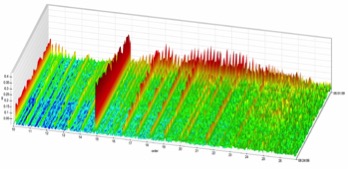
图10 14.927阶周边的3D阶次谱
从图 9 中可以看到 34 阶两边区域的阶次随时间变化没有出现幅值明显增长的现象;而图 10 则清楚地显示了 14.927 阶两边区域的很多阶次,幅值随着时间变化而逐渐增长。根据该现象可以判断,在 14.927 阶所对应的中间轴 18 齿和输出轴 77 齿这对齿 轮副出现了故障。
结合本文第 4.3 节的分析,推断故障发生在输出轴上齿数为 77 的齿轮上。
4.5 报警工况 2D 阶次谱
为再进一步确认上述诊断分析结果,对故障工况的 2D 阶次谱进行分析。选取停机 报警前 xx 分钟(以下简称时刻 I)和 xx 分钟(以下简称时刻 I)两个时刻的 2D 阶次 谱进行对比。34 阶和 14.927 阶周边的阶次谱分别参看图 11 和图 12,线代表时刻 I 的阶次谱,黑绿线代表时刻 II 的阶次谱。
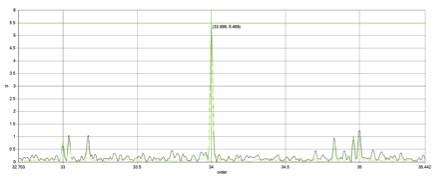
图11 34阶周边的2D阶次谱
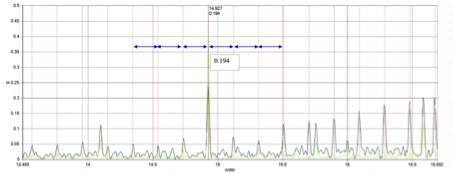
图12 14.927阶周边的2D阶次谱
从图 11 中可以看到两个时刻的阶次谱基本相同,在 34 阶两边没有出现边频带,即输入轴和中间轴的齿轮副 34/41 在整个试验过程中没有发生显著变化。
图 12 显示了在时刻 I 和时刻 II 下,14.927 阶的两边出现了等间距的边频带,幅 值呈明显增长,边频带间距为 0.194 阶。该间距与表 1 中 3 档时输出轴阶次 0.194相一致。
据此已经可以明确确认,该故障肯定是发生在 18/77 齿轮副中的输出轴上齿数为77 的齿轮上。同时,再次确认了本文第 4.3 和 4.4 节诊断分析的结果。
4.6 拆解情况
在停机报警后试验台架多次运转,工程师听到有异响对故障确认后,对变速箱进行 了拆解,在输出轴的齿数为 77 的齿轮上发现了失效,见图 13。拆解结果验证了 MIG16 SFE 的分析及诊断结果。
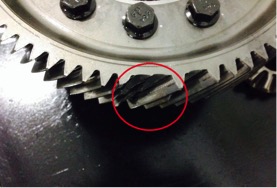
图13 拆解后77齿齿轮有断齿
5 小结
在变速箱耐久性试验过程中,MIG16 SFE 早期故障检测系统不仅检测到被试件的 失效和及时发出报警信号,而且工程师通过分析数据可以快速诊断和定位故障零部件, 指导工程师有针对性的拆解和查找故障件。
整个分析及诊断过程总结如下:
1. 查看全工况测试数据,筛选出故障工况,即故障发生时的工况为三档、转速4000rpm 和扭矩 380Nm。
2. 通过故障工况的测试数据总览,看到 OS 指标及 RMS 均方根值检测指标均呈增长趋势,并最终超出上限触发报警。
3. 通过对故障发生时的原始数据分析,可以发现明显的、周期性的冲击现象,测量该冲击现象的间隔时间为 0.077s,推测故障零部件发生在输出轴。
4. 在故障工况的 3D 阶次谱下,分析该工况下的各零部件阶次及其边频带是否有明 显的增长现象,可以看到 18/77 这对齿轮的啮合阶次 14.927 阶周边边频带明显增长,判断故障零部件为输出轴上的齿数为 77 的齿轮。
5. 为进一步确认故障零部件,最后还对比分析了停机报警前的两个不同时刻 2D 阶次谱,14.927 阶两侧的边频带间距为 0.194 阶,与输出轴的阶次相一致,最 终确定了故障零部件的位置。